Model 802005 5.4 SCFM E-Vac Low Vacuum Generator Deluxe Kit (Porous)
Applications
- Pick and place of parts and equipment
- Bag/package opening
- Label placement
- Vacuum forming
- Mold evacuation
- Vacuum filling
- Leak testing
- Evacuate containers
- Clamping and chucking
- Paper alignment and feed in printing equipment
- Vacuum packaging
- Surface mounting
- Vacuum press for wood veneers and laminates
- Carton forming
- Robotic tooling
- Vacuum liquids for testing
Advantages
- Compact, portable
- Single stage design eliminates fluctuations in vacuum
- Quiet
- Instantaneous vacuum
- Easy to mount at point of use
- Lightweight, rugged
- No moving parts – no maintenance
- 18 models
- Fast response – increases cycle time
- Durable 6061 aluminum construction
- Safe operation – no electricity
Low Vacuum In-Line E-Vac Vacuum Generators for Porous Applications
Choose the E-Vac by the SCFM (SLPM) flow that best suits the performance needed for your application.
E-Vac Kits give you the ability to experiment with an assortment of Vacuum Cups. E-Vac Kits include a Muffler, an assortment of (4) pairs of Vacuum Cups (closely matched to the performance of that E-Vac), (2) straight, (2) elbow and (1) tee vacuum fittings, 10' of vacuum tubing and a mounting clip.
Deluxe Kits include the same items as the standard kit with the addition of an automatic drain filter separator for the compressed air supply and pressure regulator (with coupler).
Airflow | In-Line E-Vac Only | In-Line E-Vac with Straight Through Muffler | In-Line E-Vac Kit with Straight Through Muffler | In-Line E-Vac Deluxe Kit with Straight Through Muffler |
1.5 SCFM 43 SLPM | 800001 | 800001M | 801001M | 802001M |
2.1 SCFM 60 SLPM | 800002 | 800002M | 801002M | 802002M |
3.1 SCFM 88 SLPM | 800003 | 800003M | 801003M | 802003M |
5.4 SCFM 153 SLPM | 800005 | 800005M | 801005M | 802005M |
8.4 SCFM 238 SLPM | 800008 | 800008M | 801008M | 802008M |
12.6 SCFM 357 SLPM | 800013 | 800013M | 801013M | 802013M |
16.8 SCFM 476 SLPM | 800017 | 800017M | 801017M | 802017M |
Note: Replace 'M' with 'H' for Standard Muffler |
Accessories
EXAIR offers a variety of mufflers, tubing, check valves, and fittings that make it easy to build a vacuum system best suited to your vacuum application. In addition to these E-Vac vacuum generator accessories, there are other items that can help with the preparation and control of the compressed air.
When using E-Vac vacuum generators, it is important to use a source of clean, dry compressed air that will keep them operating at their peak performance. Automatic Drain Filter Separators keep compressed air free of contaminants and moisture. Oil removal filters that remove oil particulate that is common to many compressed air systems are also shown. Pressure regulators, shutoff valves, compressed air hose, fittings, and solenoid valves (to electrically turn the compressed air on and off) are also available.
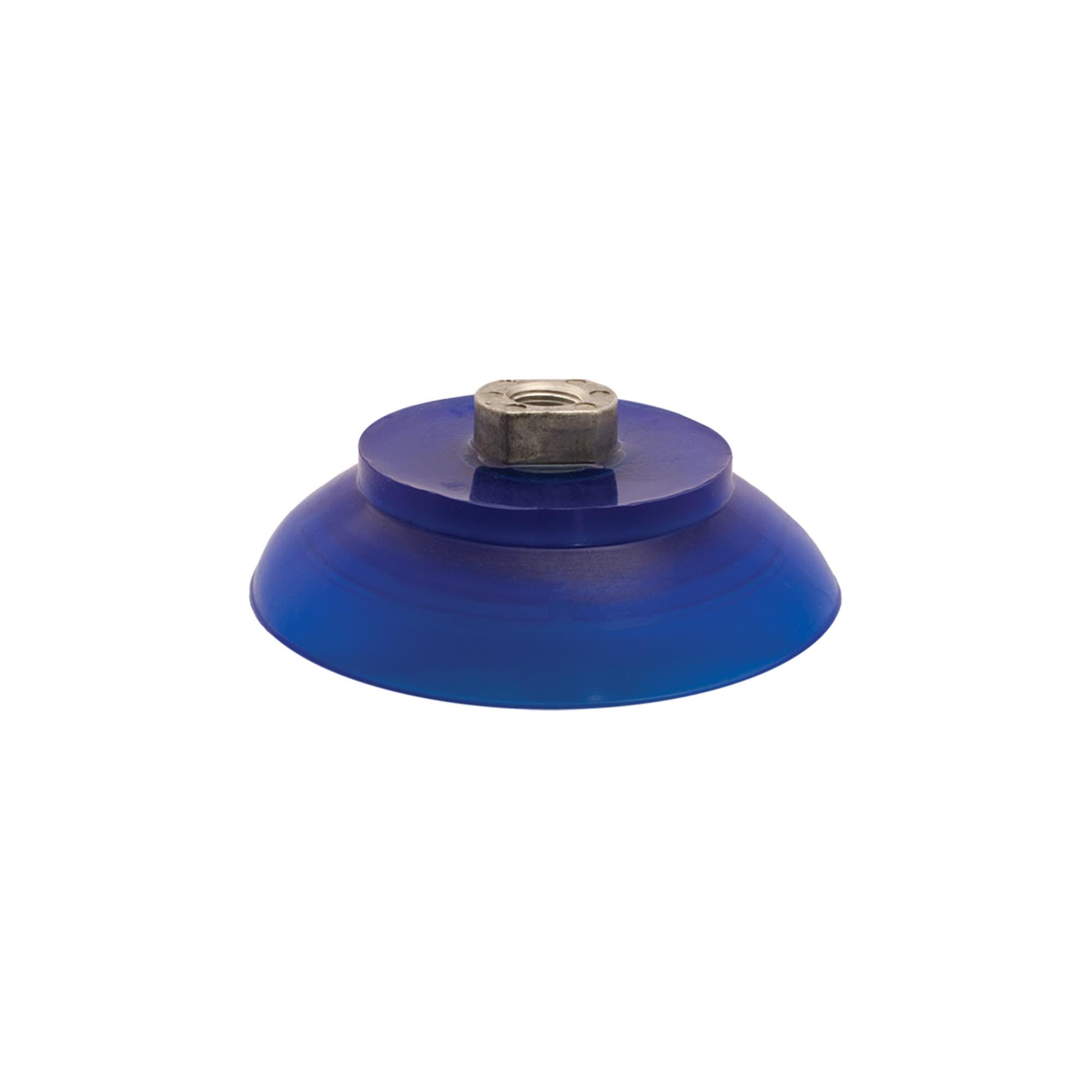
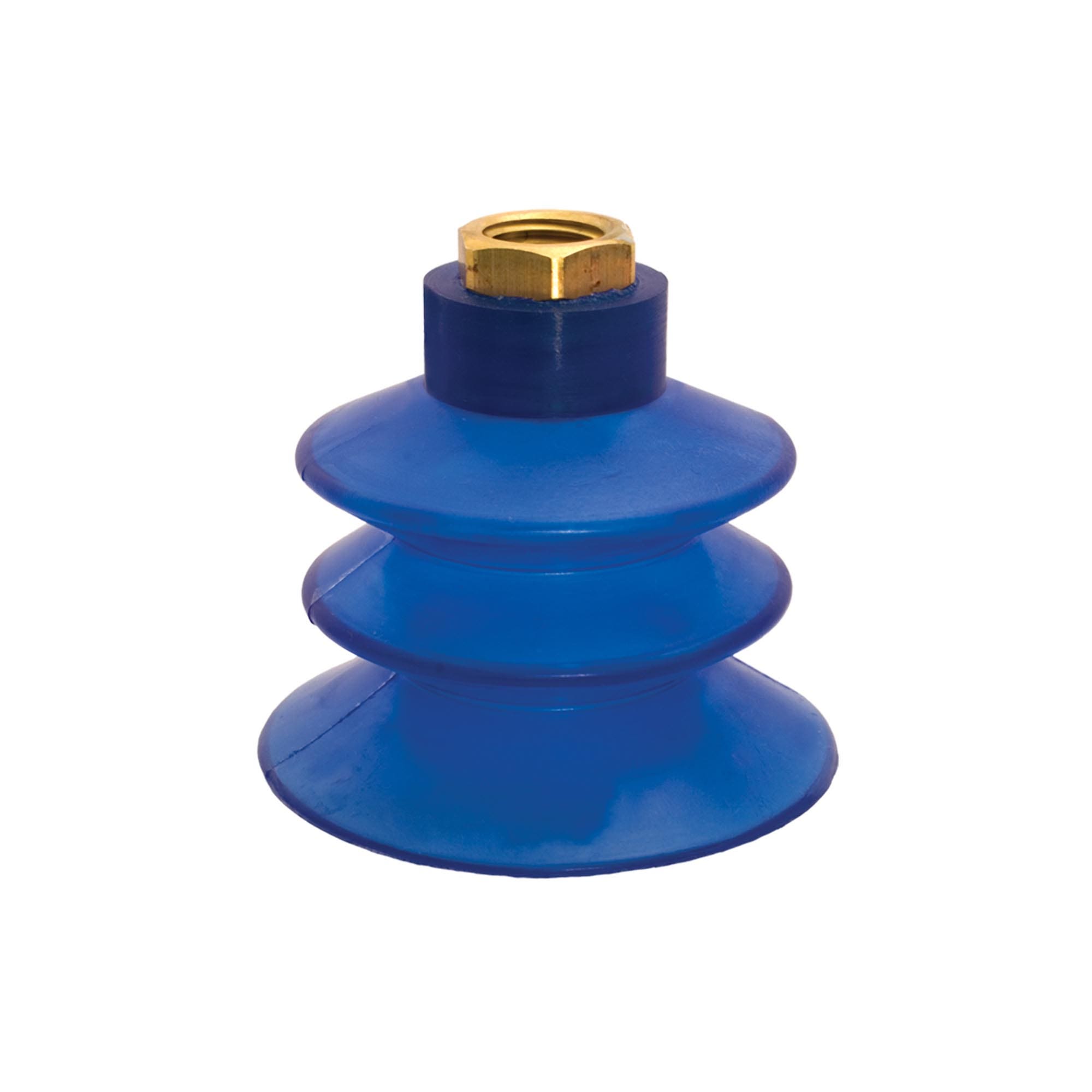
Vacuum Cups - EXAIR offers vacuum cups in a wide variety of sizes and shapes to meet the needs of your application. EXAIR's vacuum cups are made of vinyl that is ideal for geneeral purpose applications and provides excellent resistance to wear. The Durometer rating (used to indicate the flixibility and stiffness of the cup) is A50. The operating temperature is 32°F (0°C) to 125°F (51.7°C).
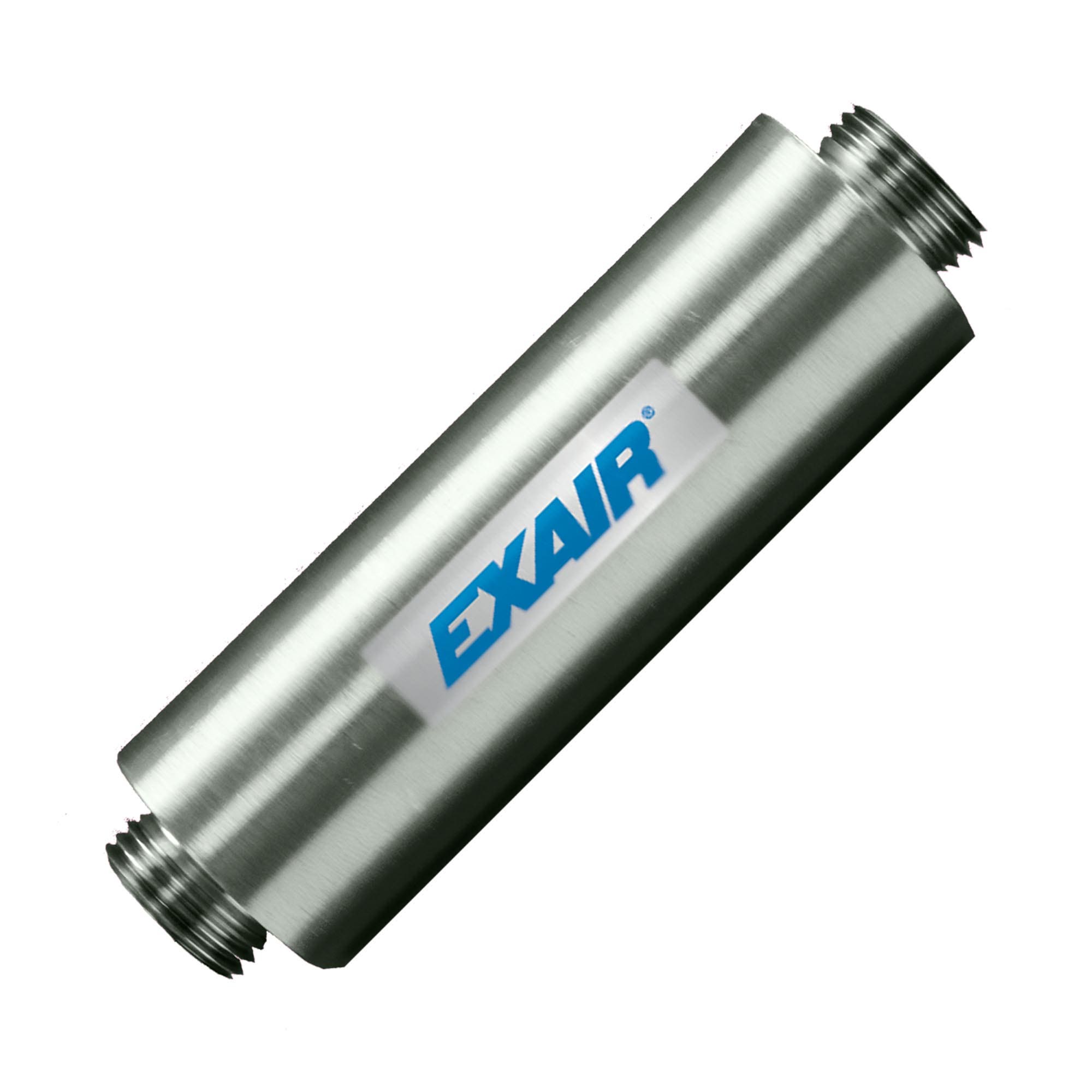
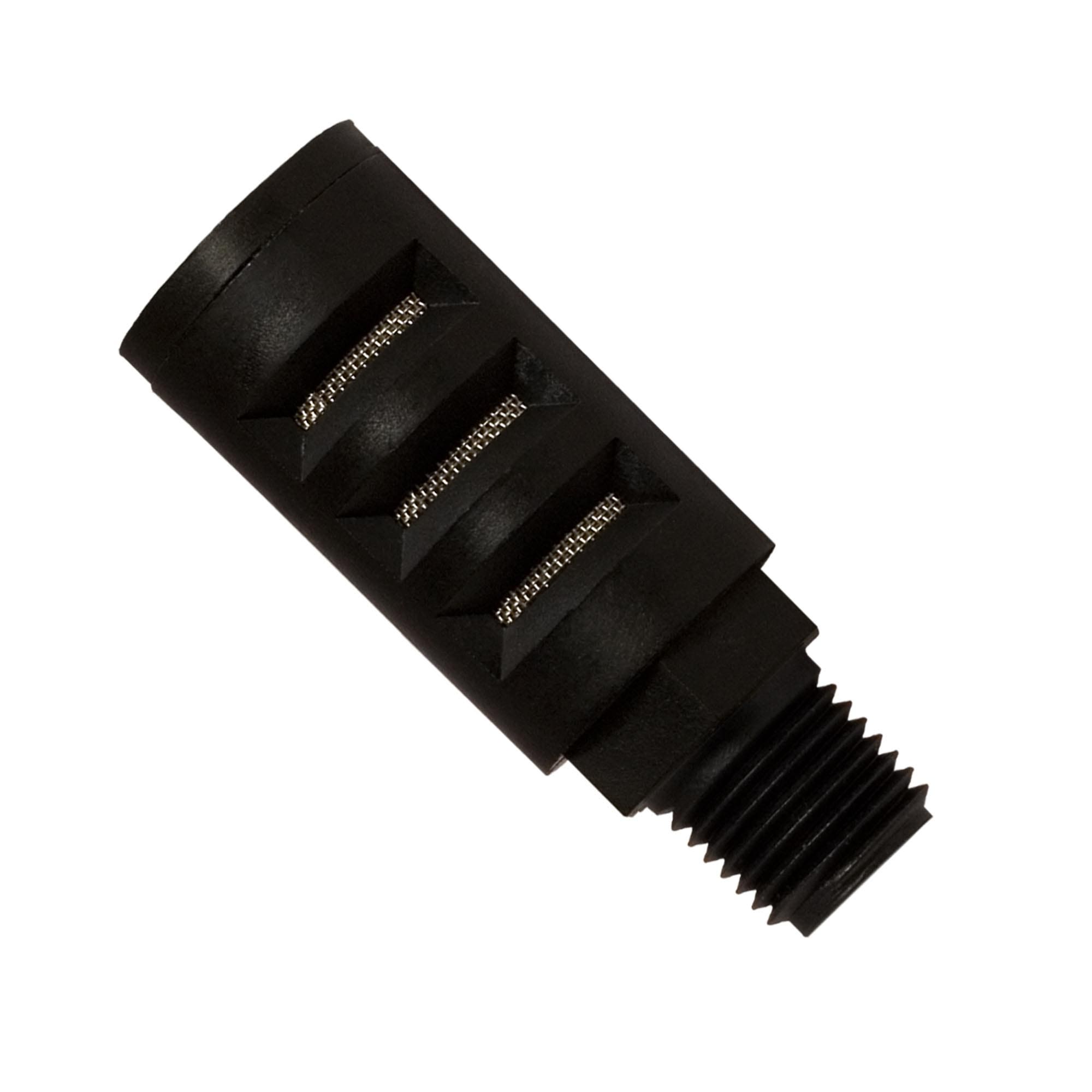
Mufflers - Optional silencing mufflers are available that permit maximum exhaust of the E-Vac unit so cycle speed is not reduced. The Standard Muffler (for use with In-Line E-Vacs only) has a closed end and is suitable for applications that are free of dust and debris. The Straight Through Muffler is recommended where particulate is present since it will not accumulate debris that can erode performance. Straight Through Mufflers offer the best sound level reduction (up to 26 dBA).
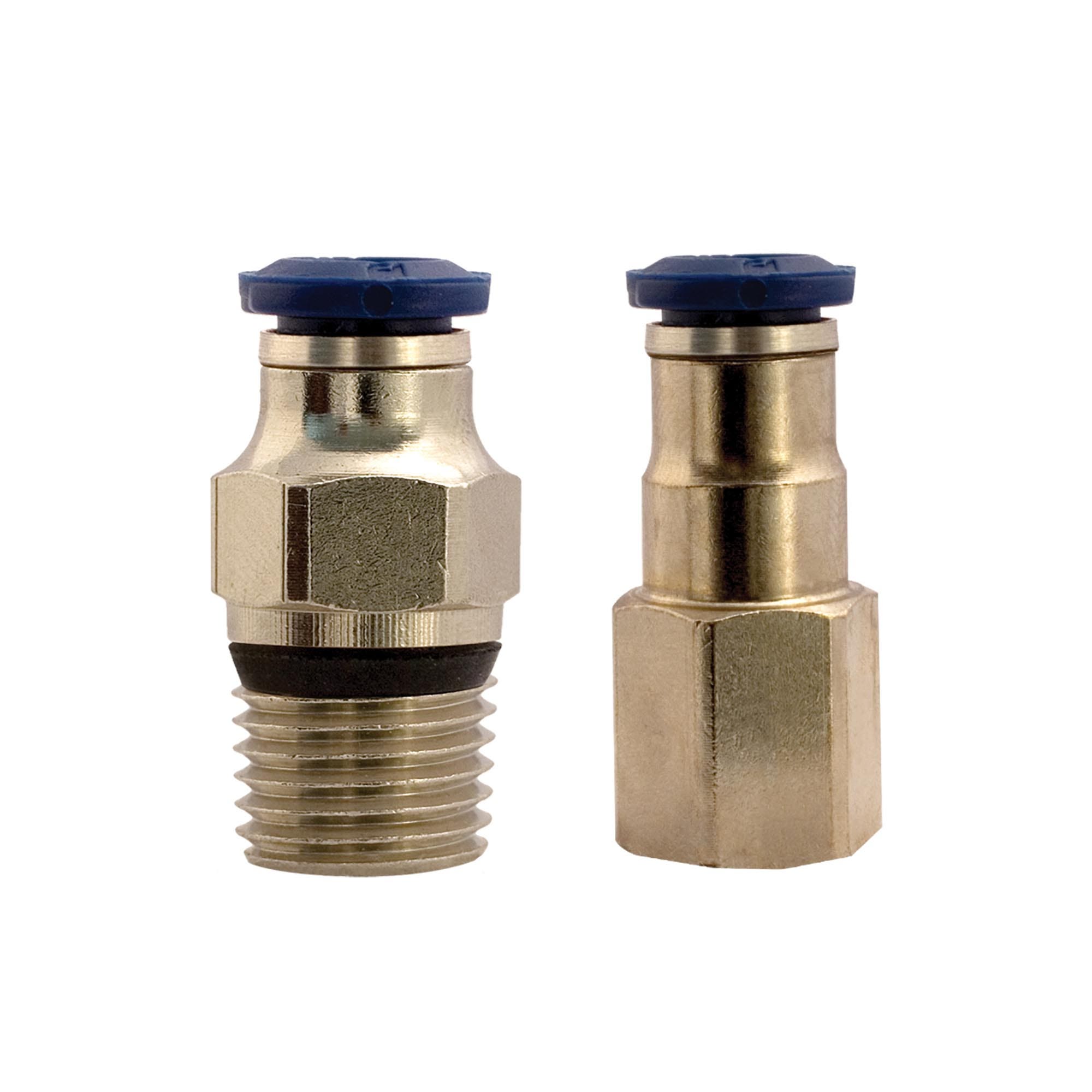
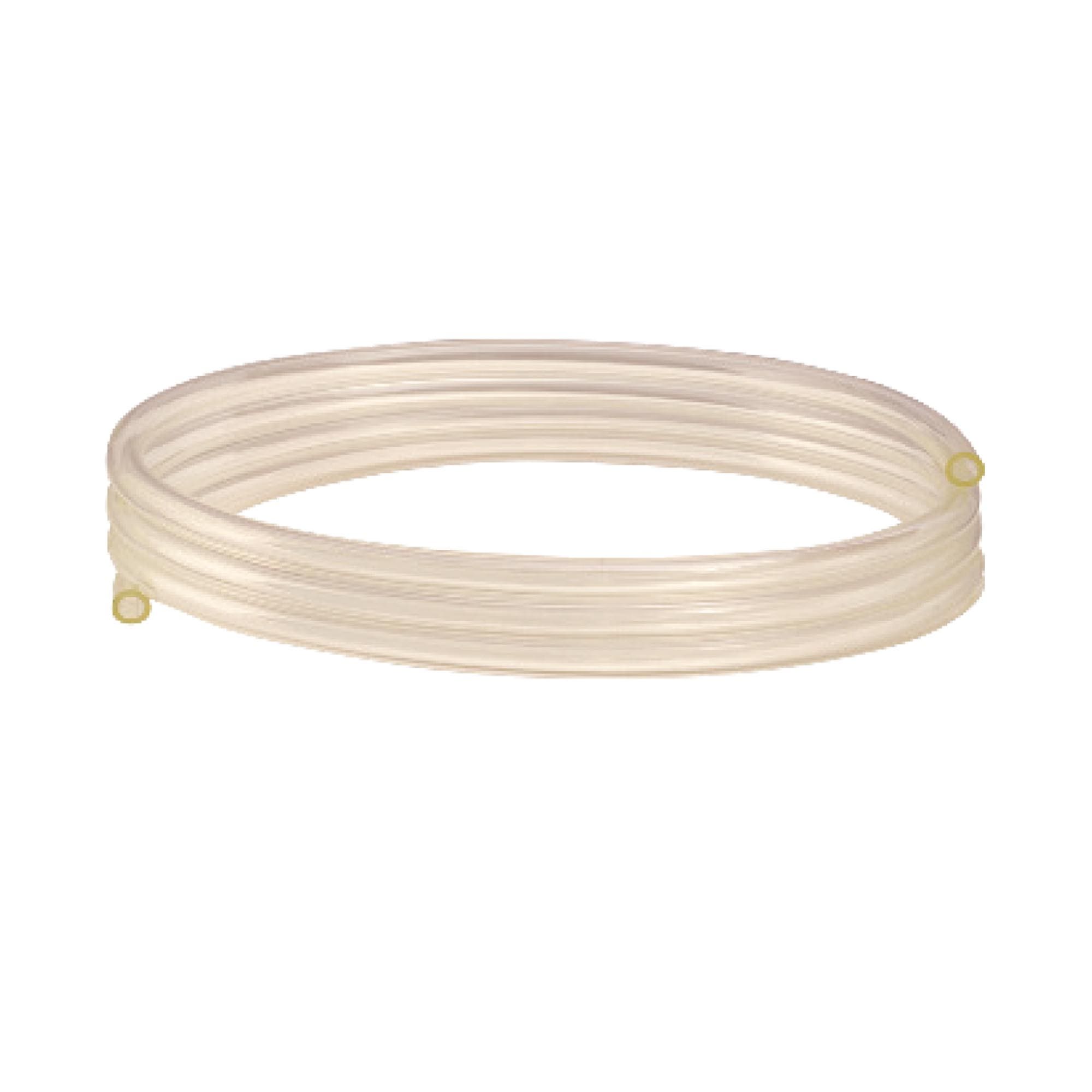
Fittings and Tubing - The vacuum port of the E-Vac has an NPT thread (a vacuum cup can be threaded directly into it). For vacuum cups that are remotely located, push-in connector fittings (most have global threads for use with NPT and BSP) can be installed on the E-Vac and the vacuum cup. Polyurethane vacuum tubing is available (10', 20', 30', 40' and 50' lengths) to connect them. For best performance, the length of the tubing should be minimized to achieve the best attach and release times.
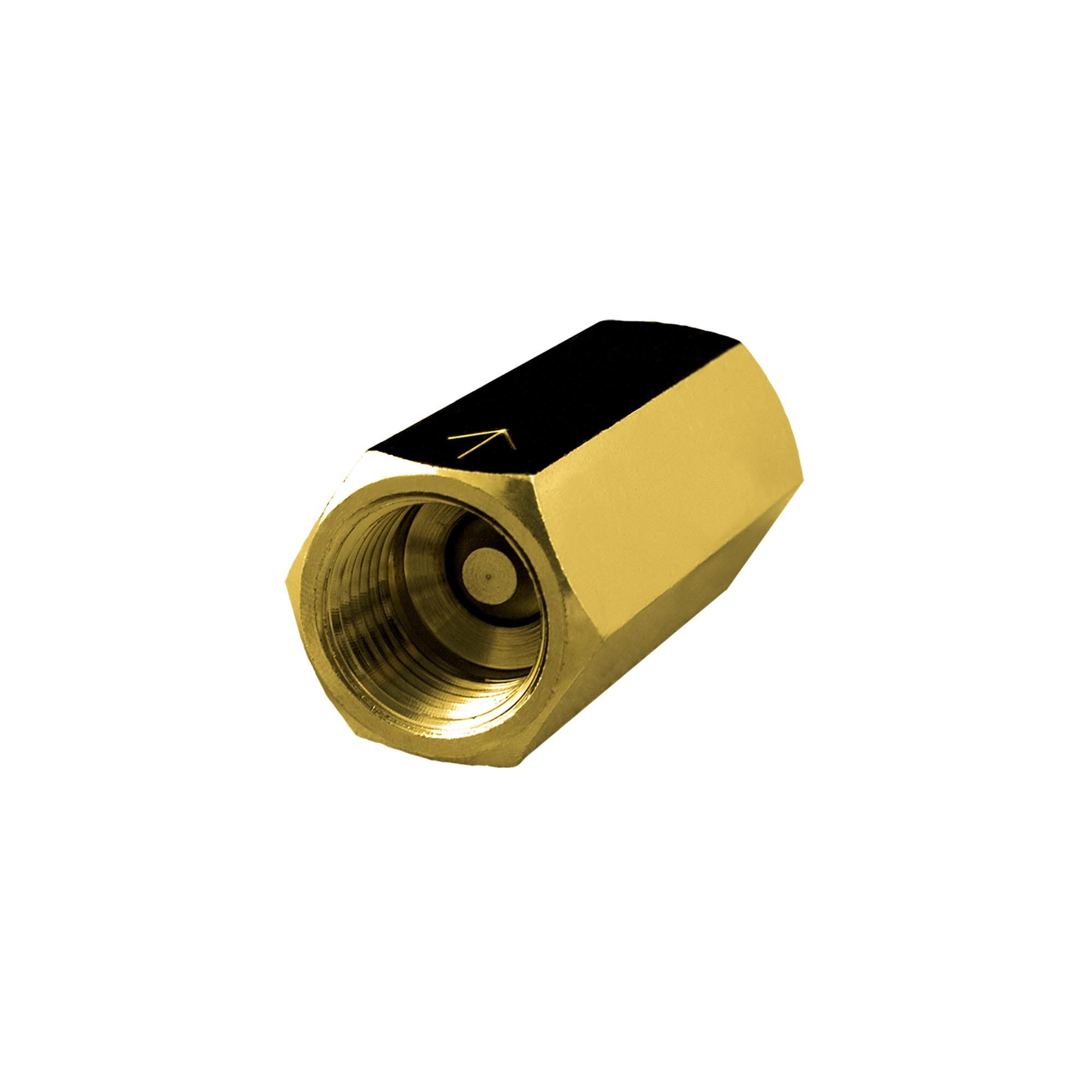
Check Valve - A vacuum check valve is available to hold the vacuum in case of compressed air loss. It is designed for high flow so it doesn’t restrict airflow or slow the vacuum operation. Maximum vacuum can still be achieved without affecting the performance. E-Vac vacuum generators that are used without a check valve will release the load if there is a significant drop in compressed air pressure or the supply of compressed air is lost.
E-Vac Styles
In-Line E-Vac Vacuum Generator
These single stage, cylindrical units are compact and easy to mount at the point of use. They can be held in place by threading them directly onto a compressed air line or with the use of a mounting clip. There are 7 models available for use with porous materials like cardboard, with vacuum levels up to 21" Hg (71 kPa) and vacuum flows up to 18.5 SCFM (524 SLPM). There are 7 models available for use with non-porous materials such as glass, with vacuum levels up to 27" Hg (91 kPa) with vacuum flows up to 15.8 SCFM (447 SLPM).
Adjustable E-Vac Vacuum Generator
This series of vacuum generators permits easy adjustment by simply loosening the locknut and turning the exhaust to increase or decrease the level of vacuum and vacuum flow. This style is also an excellent choice where large particulates may be present and passed through the vacuum system. There are 4 models with adjustable vacuum up to 25" Hg (85 kPa) and vacuum flow up to 81 SCFM (2,294 SLPM).
High vacuum units up to 27" Hg (91 kPa) are typically used for non-porous materials such as glass, steel sheet, and plastic.
In-Line E-Vac Low Vacuum Generator Performance (Porous) | |||||||||||||
Model | Air Consumption SCFM @ 80 PSIG | Sound Level in dBA | Vacuum Flow SCFM vs. Vacuum Level “Hg | ||||||||||
No Muffler | Std. Muffler | Straight Through Muffler | 0 | 3 | 6 | 9 | 12 | 15 | 18 | 21 | Max Vac | ||
800001 | 1.5 | 80 | 72 | 60 | 1.52 | 1.41 | 1.00 | 0.90 | 0.87 | 0.74 | 0.56 | 0.46 | 21 |
800002 | 2.1 | 80 | 72 | 63 | 2.22 | 2.05 | 1.48 | 1.24 | 1.09 | 1.02 | 0.78 | 0.67 | 21 |
800003 | 3.1 | 89 | 74 | 70 | 3.75 | 3.52 | 2.26 | 2.05 | 1.87 | 1.59 | 1.13 | 0.92 | 21 |
800005 | 5.4 | 92 | 83 | 66 | 5.59 | 5.23 | 3.75 | 3.15 | 2.75 | 2.39 | 1.75 | 1.27 | 21 |
800008 | 8.4 | 97 | 88 | 74 | 7.70 | 6.95 | 5.81 | 4.89 | 4.12 | 3.51 | 2.61 | 1.92 | 21 |
800013 | 12.6 | 99 | 91 | 78 | 15.50 | 14.50 | 10.45 | 9.02 | 8.10 | 6.52 | 4.54 | 3.65 | 18 |
800017 | 16.8 | 101 | 91 | 81 | 18.50 | 17.20 | 12.67 | 11.12 | 10.25 | 7.97 | 5.98 | 5.04 | 18 |
In-Line E-Vac Low Vacuum Generator Evacuation Time (Porous) | |||||||||
Model | Air Consumption SCFM @ 80 PSIG | Time in seconds to evacuate a 1 cubic foot container down to listed vacuum (shown in "Hg). | |||||||
0 | 3 | 6 | 9 | 12 | 15 | 18 | 21 | ||
800001 | 1.5 | 0.00 | 3.30 | 7.95 | 14.40 | 22.90 | 34.55 | 52.75 | 137.45 |
800002 | 2.1 | 0.00 | 2.40 | 5.35 | 9.25 | 14.30 | 22.65 | 35.05 | 105.5 |
800003 | 3.1 | 0.00 | 1.45 | 3.10 | 5.60 | 9.10 | 15.60 | 34.05 | 92.30 |
800005 | 5.4 | 0.00 | 0.80 | 2.00 | 3.50 | 5.65 | 8.70 | 15.65 | 39.90 |
800008 | 8.4 | 0.00 | 0.70 | 1.60 | 2.80 | 4.40 | 6.95 | 14.70 | 29.35 |
800013 | 12.6 | 0.00 | 0.31 | 0.81 | 1.36 | 2.16 | 3.51 | 11.21 | N/A |
800017 | 16.8 | 0.00 | 0.31 | 0.71 | 1.26 | 2.06 | 3.41 | 8.06 | N/A |
In-Line E-Vac Low Vacuum Generator Performance (Porous) - Metric | |||||||||||||
Model | Air Consumption SLPM @ 5.5 BAR | Noise Level in dBA | Vacuum Flow SCFM vs. Vacuum Level kPa | ||||||||||
No Muffler | Std. Muffler | Straight Through Muffler | 0 | 10 | 20 | 31 | 41 | 51 | 61 | 71 | Max Vac | ||
800001 | 72.5 | 80 | 72 | 60 | 43.0 | 39.9 | 35.4 | 31.1 | 26.9 | 24.1 | 15.9 | 0.0 | 71 |
800002 | 59.5 | 80 | 72 | 63 | 62.9 | 58.0 | 54.1 | 50.1 | 41.1 | 26.9 | 15.9 | 0.0 | 71 |
800003 | 87.8 | 89 | 74 | 70 | 106.2 | 99.7 | 89.2 | 77.9 | 60.9 | 34.0 | 15.9 | 0.0 | 71 |
800005 | 152.9 | 92 | 83 | 66 | 158.3 | 148.1 | 127.7 | 106.2 | 94.6 | 71.1 | 35.4 | 0.0 | 71 |
800008 | 237.9 | 97 | 88 | 74 | 218.0 | 196.8 | 178.4 | 150.1 | 119.8 | 89.2 | 37.1 | 0.0 | 71 |
800013 | 356.8 | 99 | 91 | 78 | 438.9 | 410.6 | 372.4 | 321.4 | 246.3 | 114.1 | 0.0 | 0.0 | 61 |
800017 | 475.7 | 101 | 91 | 81 | 523.8 | 487.0 | 416.2 | 351.1 | 277.5 | 141.6 | 0.0 | 0.0 | 61 |
In-Line E-Vac Low Vacuum Generator Evacuation Time (Porous) - Metric | |||||||||
Model | Air Consumption SLPM @ 5.5 BAR | Time in seconds to evacuate a 0.3 cubic meter container down to listed vacuum (shown in kPa) | |||||||
0 | 10 | 20 | 31 | 41 | 51 | 61 | 71 | ||
800001 | 42.5 | 0.00 | 3.30 | 7.95 | 14.40 | 22.90 | 34.55 | 52.75 | 137.45 |
800002 | 59.5 | 0.00 | 2.40 | 5.35 | 9.25 | 14.30 | 22.65 | 35.05 | 105.5 |
800003 | 87.8 | 0.00 | 1.45 | 3.10 | 5.60 | 9.10 | 15.60 | 34.05 | 92.30 |
800005 | 152.9 | 0.00 | 0.80 | 2.00 | 3.50 | 5.65 | 8.70 | 15.65 | 39.90 |
800008 | 237.9 | 0.00 | 0.70 | 1.60 | 2.80 | 4.40 | 6.95 | 14.70 | 29.35 |
800013 | 356.8 | 0.00 | 0.31 | 0.81 | 1.36 | 2.16 | 3.51 | 11.21 | N/A |
800017 | 475.7 | 0.00 | 0.31 | 0.71 | 1.26 | 2.06 | 3.41 | 8.06 | N/A |
In-Line E-Vac Dimensions | ||||||||||||
![]() | ||||||||||||
Model | Air Inlet A | Vacuum Inlet B | C | D | E | F | G | H | J | K | ||
800001, 800002, 800003 | 1/8 NPT | 1/8 NPT | in | N/A | N/A | 3.00 | 0.88 | 0.75 | 1/4 NPT | N/A | N/A | |
mm | N/A | N/A | 76 | 22 | 19 | N/A | N/A | |||||
800001H, 800002H, 800003H | 1/8 NPT | 1/8 NPT | in | N/A | 5.00 | 3.00 | 0.88 | 0.75 | 1/4 NPT | N/A | 0.81 | |
mm | N/A | 127 | 76 | 22 | 19 | N/A | 21 | |||||
800001M, 800002M, 800003M | 1/8 NPT | 1/8 NPT | in | 5.25 | N/A | 3.00 | 0.88 | 0.75 | 1/4 NPT | 1/4 NPS | 0.75 | |
mm | 1.33 | N/A | 76 | 22 | 19 | 1/4 NPS | 19 | |||||
800005, 800008 | 1/4 NPT | 3/8 NPT | in | N/A | N/A | 4.50 | 1.50 | 1.00 | 3/8 NPT | N/A | N/A | |
mm | N/A | N/A | 114 | 38 | 25 | N/A | N/A | |||||
800005H, 800008H | 1/4 NPT | 3/8 NPT | in | N/A | 7.50 | 4.50 | 1.50 | 1.00 | 3/8 NPT | N/A | 1.25 | |
mm | N/A | 191 | 114 | 38 | 25 | N/A | 32 | |||||
800005M, 800008M | 1/4 NPT | 3/8 NPT | in | 7.75 | N/A | 4.50 | 1.50 | 1.00 | 3/8 NPT | 3/8 NPS | 1.00 | |
mm | 197 | N/A | 114 | 38 | 25 | 3/8 NPS | 25 | |||||
800013, 800017 | 1/2 NPT | 1/2 NPT | in | N/A | N/A | 6.00 | 1.88 | 1.25 | 1/2 NPT | N/A | N/A | |
mm | N/A | N/A | 152 | 48 | 32 | N/A | N/A | |||||
800013H, 800017H | 1/2 NPT | 1/2 NPT | in | N/A | 9.00 | 6.00 | 1.88 | 1.25 | 1/2 NPT | N/A | 1.25 | |
mm | N/A | 229 | 152 | 48 | 32 | N/A | 32 | |||||
800013M, 800017M | 1/2 NPT | 1/2 NPT | in | 10.25 | N/A | 6.00 | 1.88 | 1.25 | 1/2 NPT | 1/2 NPS | 1.25 | |
mm | 260 | N/A | 152 | 48 | 32 | 1/2 NPS | 32 |
How The In-Line E-Vac Works | |
![]() | |
Compressed air flows through the inlet (1), then through a single directed nozzle (2). As the airstream exhausts, it expands and increases in velocity prior to passing through the venturi (3). A vacuum inlet tangential to the primary airflow (4) is located at the suction point between the orifice and the venturi. The airflow that is drawn through the vacuum inlet mixes with the primary airstream, then exhausts on the opposite end (5). |
In-Line E-Vac Standards and Certifications

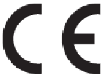
EXAIR In-Line E-Vacs comply with OSHA's Safety Requirements, the EU General Product Safety Directive (2001/95/EC) and meet the noise limitation requirements of the EU Machinery Directive (2006/42/EC). All sound level measurements are taken at 3 feet away.
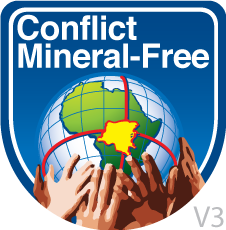
Look for this symbol to designate conflict mineral free products throughout our website. EXAIR supports Section 1502 of the Dodd-Frank Wall Street Reform and Consumer Protection Act and we are committed to compliance with the conflict minerals rule in order to curb the illicit trade of tin, tantalum, tungsten and gold in the DRC region. EXAIR is using the CMRT 3.02 template to document our supply chain and commitment to conflict free products.
How to Build An E-Vac System |
||||||||||||||||||||||||||||||||||||||||||||||||||||||||||||||||||||||
Here is an example using the steps outlined above: If it is porous, like wood, and positioned vertically:
If it is non-porous, like glass, and positioned horizontally:
|
Increased Energy and Vacuum Efficiency
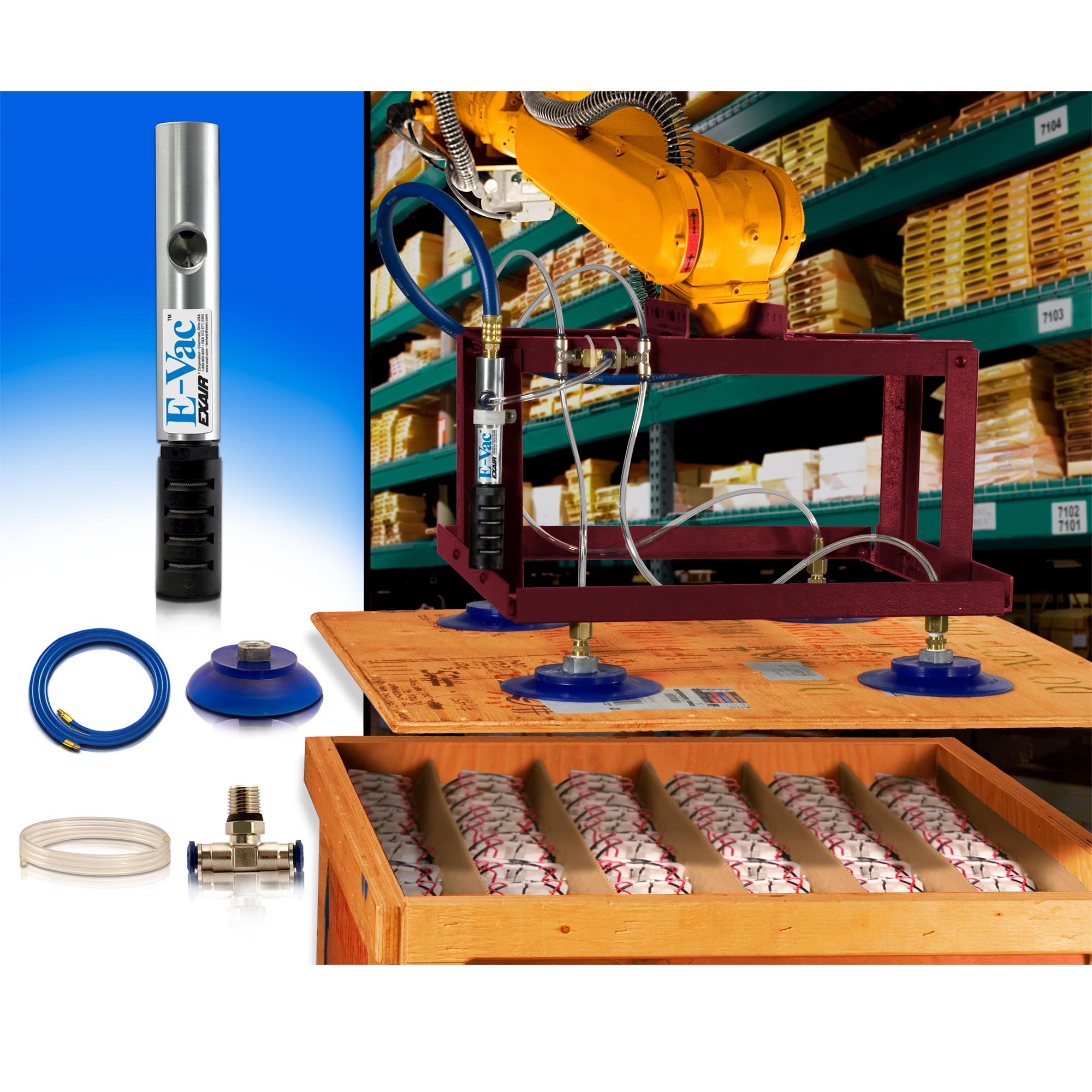
Energy and vacuum efficiency are not limited to the Adjustable E-Vac vacuum generators. All E-Vac styles and models can offer significant improvements when looking to reduce the amount of compressed air used for a specific vacuum application. Once the appropriate amount of vacuum and flow for the application are determined, it is important to select the appropriate model that will deliver the best performance while using the least amount of compressed air that it takes to do the job.
Many companies have a centralized vacuum system where the vacuum is generated at a location that is far away from the point of use. The long runs of piping through the plant produce line loss and it is often difficult to obtain that perfect balance of vacuum and flow required for an application. The compact In-line E-Vac vacuum generators eliminate this problem since they can be mounted at the point where the vacuum source is needed. EXAIR’s Application Engineers can help you to select the E-Vac vacuum generator and vacuum cups that provide the right amount of lifting capability while minimizing the amount of compressed air usage.
Other Applications for the E-Vac
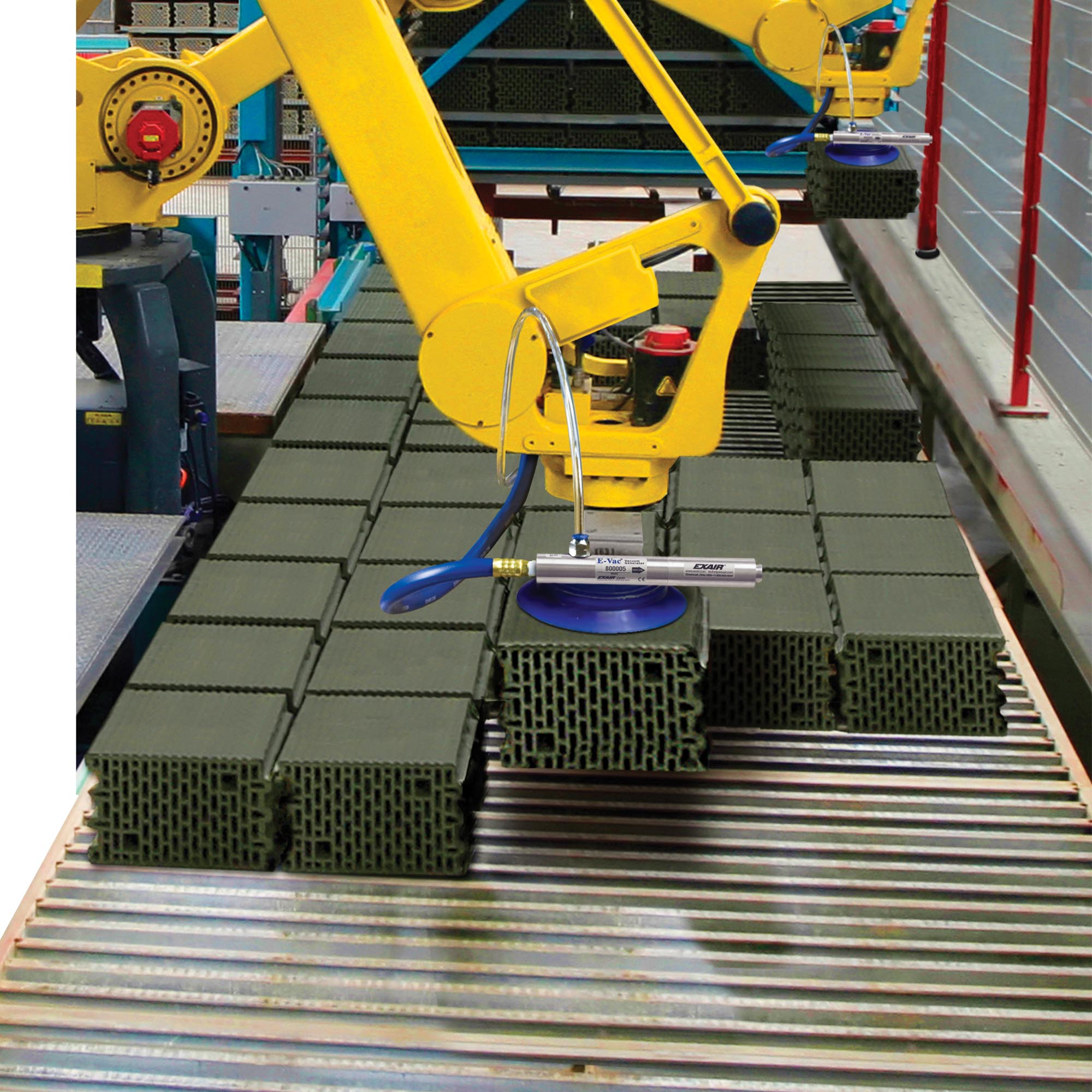
E-Vacs are used in many other “non-lifting” applications. They are commonly used for vessel evacuation, clamping, chucking, and other work holding applications. Many types of automated equipment use vacuum to evacuate, grip, hold, align and insert parts. These vacuums can be used for surface mounting, vacuum packaging, bag opening, label placement, carton forming and container evacuation.
Another popular application is using the E-Vac for liquid sampling. This process can easily be accomplished using an E-Vac vacuum generator attached to a liquid holding tube. When the tube is dipped into the vat, tank or container, the compressed air is turned on so it draws a specific volume of liquid up into the tube. When the compressed air is turned off , the liquid flows from the tube and can be dispensed into a container or machine to be analyzed.
-
Model 802005 5.4 SCFM E-Vac Low Vacuum Generator Deluxe Kit (Porous)